Mitsubishi Electric ha lanciato due modelli della stampante 3D in metallo a filo-laser AZ600, che fonde un filo per saldatura con un fascio laser per creare strutture 3D di alta qualità.
I nuovi modelli, grazie alla tecnologia di produzione additiva digitale unita a un controllo spaziale simultaneo su 5 assi e al controllo coordinato delle condizioni di lavorazione, assicurano una stampa 3D stabile e di alta qualità.
Inoltre, permettono di ridurre l’impronta ecologica dei processi di produzione, con un ritorno economico per le aziende. Infatti, la riduzione dell’energia necessaria alla stampa, consente di risparmiare risorse riducendo i tempi di lavorazione e utilizzando metodi di produzione estremamente efficienti come la formatura “near-net-shape”.
I nuovi modelli supportano anche il riporto per la saldatura di riparazioni per la manutenzione di componenti specializzati per automobili, navi e aerei. A questo si aggiunge un nuovo servizio di stampa in appalto che utilizza queste stampanti e che favorirà l’adozione della produzione additiva, offrendo consulenze sulla progettazione dei prodotti, prototipazione e consigli generali sull’applicazione della stampa 3D in metallo.
Indice degli argomenti
Il bisogno di sostenibilità traina l’adozione della stampa 3D
Negli ultimi anni, la necessità crescente di ridurre le emissioni di CO2 nel settore della lavorazione dei metalli ha accelerato la domanda di metodi di lavorazione più efficienti, in grado di ridurre il consumo energetico e conservare risorse naturali finite.
Un trend che l’azienda prevede affermarsi ulteriormente nel futuro, soprattutto per quanto riguarda la crescita della domanda di stampanti 3D in metallo, che creano oggetti a partire dai dati delle forme tridimensionali.
I vantaggi di questa tecnica sono la riduzione significativa dei tempi e dei materiali di scarto del processo di produzione e il miglioramento della flessibilità di progettazione, facilitando l’integrazione di più parti e la riduzione del peso.
D’altro canto, le stampanti 3D in metallo che utilizzano materie prime in polvere presentano problemi di gestione dei materiali, lavorabilità e sicurezza. Problemi che trainano il bisogno di un nuovo processo di produzione additiva.
AZ600, la stampante in metallo a filo-laser di Mitsubishi Electric
Per risolvere i problemi delle stampanti a polvere, Mitsubishi Electric lancia AZ600, la prima stampante 3D in metallo a filo-laser al mondo che combina il controllo spaziale simultaneo su 5 assi e una tecnologia di produzione additiva digitale che controlla in modo preciso e cooperativo le condizioni di lavorazione.
Questo prodotto realizza stampe 3D di alta qualità e precisione e viene incontro alle esigenze degli operatori del settore manifatturiero consci del proprio impatto ambientale, riducendo il consumo e lo spreco di energia.
Il nuovo metodo con materia prima in fili di Mitsubishi Electric risolve i problemi di sostenibilità, conservazione e costi dei materiali che caratterizzano le stampanti 3D in metallo tradizionali, grazie all’utilizzo di un fascio laser, che permette un controllo estremamente preciso della quantità di calore immessa in base allo stato della fabbricazione, combinando in tal modo la precisione dello stampaggio con i vantaggi della materia prima in fili.
L’uso esclusivo di un controller numerico computerizzato (CNC) per il controllo cooperativo delle condizioni di lavorazione, quali l’avanzamento del filo, la potenza del laser e l’avanzamento dell’asse, rende possibile la produzione additiva di strutture tridimensionali di alta precisione e alta qualità.
Ottimizzando il controllo dei valori dei comandi dell’asse, della quantità di avanzamento del filo e dei valori dei comandi di potenza del laser in base ai dati sullo stato della fabbricazione forniti da sensori, si ottiene un processo di fabbricazione altamente stabile per una stampa 3D di alta qualità.
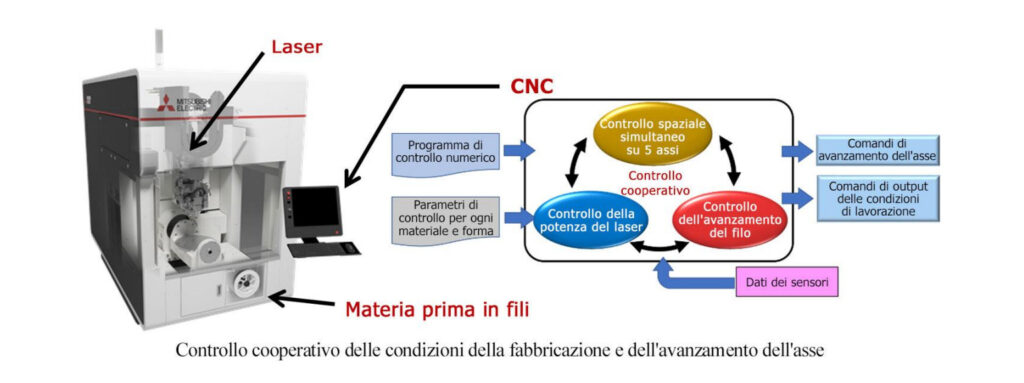
Inoltre, l’applicazione della tecnologia di stampa digitale per il controllo dell’intensità e della potenza del fascio laser e dell’avanzamento del filo con la tecnologia CAM (produzione assistita dal computer) dedicata per la generazione del percorso di stampa consente di ottimizzare le condizioni della fabbricazione in base a strutture tridimensionali specifiche, utilizzando formatura a punti o continua.
L’uso di materie prime in fili di qualità uniforme contribuisce a una formatura del metallo di alta qualità per creare strutture ad alta densità con pochi vuoti. Le strutture tridimensionali complesse, difficili da realizzare utilizzando una fonte di calore ad arco, possono essere formate in modo molto accurato utilizzando l’esclusiva tecnologia di controllo del calore ad alta precisione di Mitsubishi Electric.
È inoltre possibile creare sfere cave, che in linea di principio non possono essere create con le tecniche di taglio tradizionali.
I vantaggi del metodo “near the shape”
Il metodo di formatura “near-net-shape”, in cui si crea in poco tempo una forma quasi finale che viene poi rifinita mediante taglio, può ridurre i tempi di lavorazione e i materiali di scarto rispetto ai metodi convenzionali che utilizzano il taglio per tutti i processi, dalla sgrossatura alla finitura.
Nella produzione di prova di un’elica marina con un diametro di 300 mm, ad esempio, il metodo “near-net-shape” ha ridotto i tempi di lavorazione e i materiali di scarto dell’80% circa rispetto ai metodi convenzionali, che richiedono la molatura finale di tutto l’oggetto.
Inoltre, la produzione additiva può essere utilizzata nel contesto della riparazione e della manutenzione di costosi componenti di consumo, in particolare quelli utilizzati in ambienti difficili, come pale di turbine o stampi, in quanto può prolungare la durata e ridurre i costi di esercizio associati a tali componenti.
Infine, l’utilizzo di una tecnologia avanzata di controllo spaziale simultaneo su 5 assi consente di realizzare mediante la stampa 3D in metallo processi tradizionalmente manuali molto specializzati per la saldatura a riporto e a cordone, che utilizzano materiali come TIG (Tungsten Inert Gas), migliorando la qualità della struttura prodotta, riducendo i tempi di fabbricazione e risparmiando manodopera.