Il mondo non sta cambiando, il mondo è già cambiato. O almeno lo è l’economia e in particolare la catena di produzione e distribuzione, che è passata da un modello basato su una supply chain lineare, fatta di processi e passaggi rigidi, a una conformazione di “connected value chain”, con interazioni molto più complesse fra i vari stadi. Neologismi come servitization, hyper-customization, e customer centric economy sono ormai entrati nel gergo standard del marketing, a indicare un processo di produzione e vendita flessibile e non più massificato; e se nella distribuzione e vendita è visibile a tutti l’avvenuta trasformazione, con prodotti sempre più “su misura” e catena (e cliente) sempre più digitale, nella produzione si è segnato un po’ il passo, ma è chiaro che si debba percorrere lo stesso cammino. Questo il pensiero di Oracle, che ha presentato nei giorni scorsi in anteprima la sua visione della “Smart Connected Factory”, la fabbrica intelligente e connessa in cloud che dovrebbe, secondo la società di Redwood, portare la produzione ad allinearsi da un punto di vista tecnologico e filosofico con gli obiettivi della filiera di distribuzione e vendita.
Indice degli argomenti
Un mondo di Digital Enterprise
Secondo Simone Marchetti, Business Developer Manager di Oracle Italia, l’obiettivo per le aziende è trasformarsi in Digital Enterprise, per fare Digital Business con quelli che ormai sono dei Digital Customer. E i fattori chiave per riuscirci sono l’innovazione di prodotto, la logistica flessibile e soprattutto lo Smart Manufacturing, ottenibile tramite un esteso lavoro di digitalizzazione della produzione.
Verso la digital factory
Per diventare una Digital Enterprise a tutto tondo anche la produzione deve essere digitalizzata. Bisogna avere delle Digital Factory, insomma, stabilimenti di produzione che siano in grado di integrarsi perfettamente nel puzzle tecnologico dell’industria 4.0. Che è composto di tessere che vanno sotto il nome di cloud, augmented reality, big data & analytics, IT security, integrazione software, intelligenza artificiale, customizzazione, robotica.
Non si tratta, semplicemente, di sostituire nuovi macchinari a quelli attuali. Si tratta di cambiare il modo in cui umani e macchine interagiscono e imparano l’uno dall’altro, in modo da poter lavorare meglio entrambi. Si tratta di passare a un modello, come la chiama Oracle, di Smart Connected Factory.
Dentro la Smart Connected Factory
Alla base di tutto ci sono i dati: essi sono il vero carburante della Smart Connected Factory. Sensori, piattaforme e persone generano costantemente dati che la Smart Connected Factory può analizzare e tradurre in azioni attraverso un sistema fortemente automatizzato. I dati consentono l’utilizzo di ogni tipo di strumenti intelligenti e tecnologie sofisticate. Questo corrisponde ai canoni dell’industria 4.0, che deve avere caratteristiche di interoperabilità (macchine, dispositivi, sensori e persone devono essere connessi), trasparenza dell’informazione (tramite una copia virtuale del mondo fisico elaborata dai sistemi informativi), assistenza tecnica (apparecchiature digitali possono supportare fisicamente gli umani nei compiti più duri, rischiosi o semplicemente poco piacevoli) e di decentralizzazione delle decisioni (apparecchi digitali possono prendere decisioni autonomamente e svolgere i loro compiti in modo il più possibile autonomo).
Dalla teoria alla pratica
Certo, quello che abbiamo fin qui descritto pare troppo bello per essere vero. Ma Oracle ci teneva a dimostrare che questi concetti sono già stati tradotti in soluzioni concrete commercialmente disponibili. Così, con la collaborazione di Bosch Rexroth ha allestito un impianto dimostrativo di tutte queste tecnologie, e lo mostrerà al pubblico che interverrà al prossimo evento SPS Italia, che si terrà a Parma dal 22 al 24 maggio 2018. Abbiamo potuto vedere in anteprima il funzionamento di questa linea grazie a una demo virtuale tenutasi nei giorni scorsi a Milano. Durante la demo, l’impianto “fisico” di produzione è stato sostituito da un simulatore digitale, ma tutto il resto ha funzionato come nella realtà. A Parma, invece, ci sarà la demo completa, linea di produzione compresa.
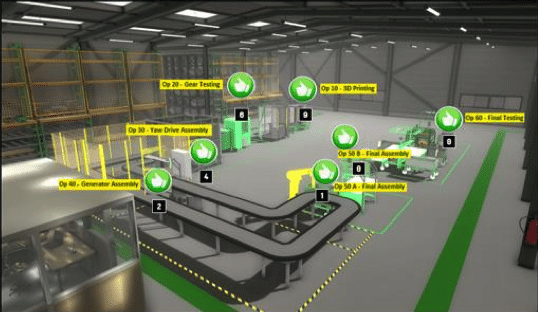
Gli elementi della Smart Connected Factory
Secondo Sergio Gimelli, Sales Consultant Director di Oracle, una cosa molto importante in ottica Smart Connected Factory è riuscire a integrare le culture IT e OT. Due culture che differiscono sostanzialmente proprio nei dati che producono. L’OT produce dati reali in tempo reale, ma difficili da usare; i dati dell’IT, d’altro canto, non sono mai in tempo reale, sono filtrati e spesso “simulati”, adatti più per il gestionale che per la gestione.
Una Smart Connected Factory, invece, dovrebbe essere IoT enabled, con le apparecchiature connesse alla applicazioni business, dotata di sistemi di machine learning e intelligenza artificiale, e resa interattiva tramite realtà aumentata e Digital Twin (un impianto virtuale gemello di quello fisico). Il tutto andrà poi interconnesso con tecnologie come i Chatbots e la Blockchain, per semplificare l’interazione e rendere sicuro l’utilizzo business. Già, perché usando il cloud con le giuste tecnologie è possibile aumentare il livello di sicurezza del sistema, come emerge da questa intervista che abbiamo fatto a Domenico Garbarino di Oracle in occasione del Security Summit del Clusit lo scorso marzo.
Il Cloud di Oracle
Tutti questi elementi possono essere forniti dalle applicazioni cloud di Oracle. La IoT Cloud Enterprise Platform, per esempio, fornisce strumenti per l’Asset Monitoring, il Production Monitoring, il Fleet Monitoring, oltre che per i Connected Worker e il Service Monitoring for Connected Assets. Le applicazioni usano tecnologie sofisticate, come il Machine Learning e il Predictive Analytics, per fornire servizi di intelligenza artificiale alla gestione della supply chain.
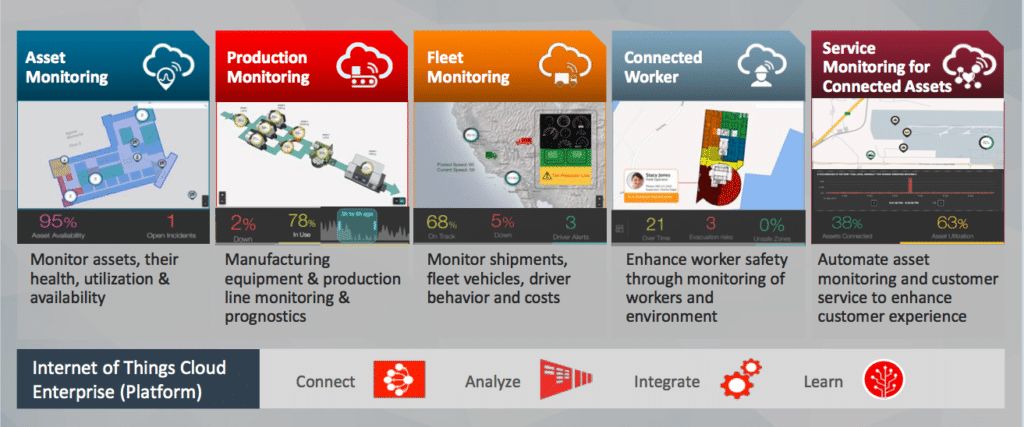
Nel segmento produzione possono per esempio localizzare anomalie, predire possibili guasti, programmare manutenzioni sulla base di modelli elaborati a partire dai dati provenienti dai sensori e dall’ERP, fornire raccomandazioni sulle azioni da intraprendere, ottimizzare l’uso dei sistemi, prevedere l’andamento della domanda.
Durante la demo, è stato mostrato come un direttore di produzione possa avere pieno controllo dello stabilimento ovunque egli si trovi, a patto di disporre di una connessione Internet e di un dispositivo mobile (un tablet per esempio). Nel caso che un sensore segnali un’anomalia, sarà quindi possibile intervenire a distanza per individuare il problema e intraprendere le azioni necessarie per correggerlo – azioni spesso suggerite direttamente dal sistema di intelligenza artificiale della applicazione, che diventerà mano a mano più intelligente grazie al machine learning.
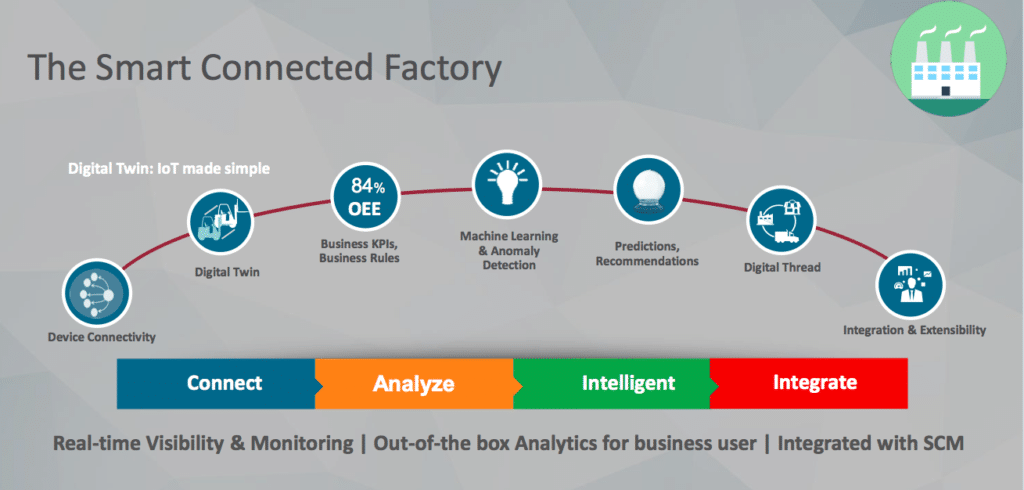
Fino al punto che l’applicazione arriverà a comunicare l’anomalia e contestualmente l’elenco delle azioni correttive ritenute necessarie, attendendo dall’operatore umano solo l’assenso a procedere per intervenire, risolvere il problema e comunicare il risultato raggiunto. Non siamo ancora ai robot che riparano altri robot, ma la strada è segnata.