Nonostante la situazione internazionale tesa fra prezzi galoppanti, il conflitto in Ucraina e la carenza di materia prime ed energia il percorso dell’automotive verso l’elettrificazione (spinto anche dalla tagliola del 2035) sembra però continuare. E in questo cammino Comau vuole essere protagonista. Ne abbiamo parlato con Paolo Tebaldi, E-Mobility Segment Leader in Comau.
Indice degli argomenti
Le batterie ACC saranno assemblate da linee Comau
L’azienda piemontese ha comunicato di aver progettato e sviluppato una linea di produzione di moduli per batterie al Litio per la futura Gigafactory di Automotive Cells Company (ACC), che sorgerà a Billy-Bercalu Douvrain, nel nord della Francia. ACC è una joint venture tra Stellantis, TotalEnergies/Saft e Mercedes–Benz, creata allo scopo di instaurare una filiera produttiva europea per le batterie dei veicoli elettrici. Uno dei poli produttivi della JV sarà a Termoli, nel riconvertito stabilimento nel quale Fiat produceva motori, ed è uno dei cardini della conversione industriale di Stellantis in Italia.
Il sistema produttivo concepito da Comau è flessibile e permette di produrre moduli da 8 e 16 celle di nuova generazione per una capacità complessiva di 8 gWh l’anno al 2024, una capacità sufficiente per 133mila veicoli ipotizzando una capacità media di 60 kWh a veicolo.
Moduli ad alta pressione
Le linee produttive saranno cinque. Di queste, tre sono capaci di produrre entrambi i moduli mentre le altre due sono specifiche per i moduli a 8 celle. È interessante notare che questa soluzione ricorre alle competenze della rete europea di Comau, in grado di garantire l’approvvigionamento locale di tecnologia, attrezzature e componenti ausiliari necessari al progetto.
Un elemento sfidante del progetto era una forza di impilamento delle celle di 300-500 decanewton (306 – 510 kg-forza) molto superiore alla media del settore di circa 100 decanewton. Per far fronte a questa specifica, gli ingegneri di Comau e ACC hanno collaborato per personalizzare il processo al fine di garantire la geometria del prodotto e le caratteristiche previste in un approccio di sviluppo congiunto (simultaneous engineering) che ha anche permesso a Comau di eliminare una delle linee originariamente previste.
Produzione end-to-end
La soluzione di Comau prevede l’automatizzazione dell’intero processo di produzione: preparazione e il collaudo delle celle prismatiche, l’impilamento, la saldatura e l’assemblaggio finale e il collaudo di fine linea. L’impegno di Comau nel settore dell’assemblaggio delle batterie si è esteso anche alle promettenti celle allo stato solido, per produrre la quali l’azienda ha sviluppato, insieme a Ilika, un processo che usa le linee pensate per le celle tradizionali.
Comau è molto impegnata in questo settore, avendo aderito anche a vari consorzi europei per lo sviluppo delle batterie di trazione tramite sistemi di produzione flessibili e digitali.
Sinergie e alleanze
In questo quadro si inserisce la recentissima adesione di Comau alla Upcell Alliance, una realtà nata in Francia che conta 36 aziende e istituzioni europee associate e che per l’Italia vede anche il Politecnico di Milano.
L’European Battery Manufacturing Alliance ha esponenti provenienti dal mondo industriale, istituzionale e accademico di diversi Paesi europei e si propone di progettare e realizzare celle, moduli e pacchi batteria allo scopo non solo di favorire l’autonomia della filiera produttiva europea ma anche di promuoverne il ruolo guida a livello globale.
Fra gli altri partner di Upcell citiamo Université Grenoble Alpes, Bühler, Technax, Schneider Electric, MTB Recycling ed Eltronic.
L’impegno di Comau nel settore dei veicoli elettrici
L’azienda piemontese, nell’orizzonte della quale c’è uno spin-off dal gruppo Stellantis, appare quindi molto interessata alla transizione della mobilità verso l’elettrificazione e l’alimentazione a fuel cell a idrogeno.
In effetti, se l’impegno più sostanziale in questo settore è iniziato nel 2019, una prima linea di assemblaggio batterie era stata consegnata circa 10 anni fa a un costruttore statunitense, prima che i grandi clienti di Comau si muovessero in forze verso l’auto elettrica.
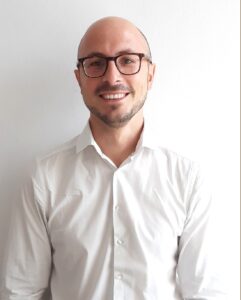
Paolo Tebaldi ha spiegato che “le lavorazioni sulle batterie sfruttano competenze nell’automazione automotive che Comau ha maturato già da diverso tempo. Attualmente l’azienda è impegnata nell’assemblaggio dei battery pack, ottenuti unendo i vari moduli che ne sono i ‘mattoni’, ma sta valutando anche sulla costruzione dei moduli, agendo quindi anche sulle singole celle. Questo orizzonte è legato alle batterie allo stato solido, che sono la quarta generazione, per realizzare le quali si è implementato un progetto con l’inglese Ilika per la produzione delle loro celle basate sulla tecnologia allo stato solido. Molto interessante nella nostra ottica è anche il testing dei moduli per assemblare batterie in second life”.
Comau pensa anche alle batterie ‘extra serie’
La produzione delle batterie agli ioni di Litio attualmente è destinata in gran parte agli autoveicoli per i quali Comau produce anche automazione destinata ai loro powertrain.
Un recente accordo con Geely, gruppo cinese proprietario anche di Volvo e del marchio premium Zeekr, vede Comau ad aver fornito, a Geely Veremt, una linea di assemblaggio automatizzata per motori elettrici, cambi e inverter.
Questo sistema di produzione flessibile assembla i rotori dei motori a magneti permanenti, cambi, le elettroniche implementa anche controllo qualità e test automatizzati e prevede anche, ad esempio, la pressatura automatica dei cuscinetti, l’alimentazione e il serraggio automatico dei bulloni, la misurazione e la selezione automatica delle guarnizioni.
Paolo Tebaldi ha anche spiegato che “è di interesse per Comau anche il settore delle batterie ‘specialistiche’ destinate per esempio al settore navale, ferroviario e dei trasporti pesanti. Un esempio è lo sviluppo, per Lechanché, di una linea automatizzata per la produzione di moduli batteria agli ioni di Litio dedicati al settore navale. È possibile gestire l’intero processo di produzione delle batterie – dall’impilamento delle celle pouch fino alla saldatura e all’assemblaggio finale. Un sistema di visione brevettato, basato sull’AI, convalida in automatico la resistenza elettromeccanica di ogni singolo punto saldato mentre la linea è integrata con la piattaforma interattiva in.GRID MES che permette un costante scambio di informazioni fra le singole celle di produzione e la linea completa”.

Dalle batterie alle fuel cell
La trazione elettrica può trarre energia anche dalle fuel cell alimentate con Idrogeno, un’altra soluzione a zero emissioni locali. Il manager di Comau ha spiegato che “le celle a combustibile hanno caratteristiche tali che il loro assemblaggio dev’essere automatizzato anche se la produzione non è in grande serie. La lavorazione di un loro stack si presta infatti bene a processi automatici ad alta velocità, competenze che Comau ha ormai da molto tempo”.
Questo settore è promettente, sia per gli usi di questo gas come vettore pulito di energia sia perché il rifornimento dell’Idrogeno è molto più veloce della ricarica di una batteria e promette elevata autonomia, caratteristiche importanti per il trasporto commerciale. Comau mette a frutto la sua expertise per processi quali la preparazione e l’impilamento delle celle, i test di tenuta e altro ancora, in un impegno a ridurre il prezzo della produzione di celle a combustibile e degli elettrolizzatori, che sono i macchinari che scindono l’acqua nei suoi componenti Idrogeno e Ossigeno.
L’azienda piemontese sta collaborando con la Shanghai Hydrogen Propulsion Technology, controllata di SAIC Motor le cui fuel cell a Idrogeno sono utilizzate in automobili, autobus, camion da leggeri fino a pesanti, carrelli elevatori e diverse altre applicazioni. Comau è inoltre coinvolta in un progetto pilota per la produzione di elettrolizzatori nella regione EMEA e in altre opportunità in Oceania.
Una domanda che non conosce pause
L’azienda ha uno sguardo privilegiato sulle tendenze dell’automotive grazie ai suoi accordi e agli ordinativi e, nonostante le tensioni internazionali, “non solo non vediamo alcun rallentamento nel cammino verso l’elettrificazione ma ipotizziamo addirittura una possibile mancanza di offerta di sistemi di automazione per la produzione delle batterie a fronte di una domanda in rapida espansione, almeno per quel che riguarda USA ed Europa per il prossimo anno. Gli eventi bellici, l’impennata nei prezzi e il cambiamento climatico stanno spingendo l’EU a cambiare il proprio mix energetico per averlo più pulito e autonomo”.
A Tebaldi abbiamo anche domandato se i costi di produzione di una BEV potrebbero scendere molto se le batterie diventassero più economiche. In effetti, ci ha detto, “la cinese BYD ha comunicato di aver raggiunto la parità con le ibride, anche perché i livelli tecnologici e di sicurezza sono diversi rispetto a quelle europei e statunitensi. Questo livellamento potrebbe essere effettivo o derivare dalla disponibilità a vendere con marginalità molto basse o nulle per poi recuperare in seguito ma ad oggi un’elettrica continua a essere più costosa da produrre di una vettura con motore a scoppio. Se il costo delle batterie scendesse molto le elettriche sarebbero più economiche delle automobili con motore a combustione perché i motori elettrici e l’elettronica sono ormai componenti maturi e meno complessi rispetto ai powertrain convenzionali. È poi da rimarcare che si tende ad allungare il controllo della catena del valore, con diversi Gruppi OE che puntano a riciclare i componenti delle auto – le batterie sono molto importanti in questo senso – e a prolungarne la vita persino sostituendo i powertrain con altri meno inquinanti, al limite elettrici”.
Più auto elettriche, meno robot?
Questa semplicità costruttiva potrebbe diminuire il ricorso ai robot per l’assemblaggio? La domanda semi-provocatoria ha ricevuto una risposta chiara: ”in Comau riteniamo che la maggiore semplicità delle auto elettriche non arriverà a limitare l’uso dell’automazione perché si tratta di vasi comunicanti: se la crescente diffusione dei Megacast, per esempio, ridurrà il numero delle saldature si farà più ricorso al machining e quindi si potrà avere meno robotica e più automazione. Ad oggi ritengo però che il ricorso all’automazione non diminuirà, anzi: la produzione crescerà molto e quindi ci sarà più lavoro per le aziende del settore”.
Questa transizione – per esempio dal motore a combustione a quello elettrico e dalla scocca saldata ai megacasting – riguarda anche la forza lavoro e in effetti in Comau già dal 2019 è iniziato un importante percorso di formazione, incentrato su reskilling e upskilling, che ha già interessato 800 addetti compresi quelli dell’engineering. Le attività connesse si estendono anche alle Università, con dottorati di ricerca e altre attività simili, ma è anche importante l’adesione ai progetti europei che, oltre a essere finanziati, permettono di conoscere altre realtà in un proficuo scambio di esperienze e competenze.