Per imprenditori, manager, operatori di produzione e studenti da un lato, ricercatori e tech provider dall’altro, le cinque “live demo” realizzate dal Competence center Smact nel Nord-Est a Bolzano, Rovereto, Padova, Verona e in Friuli Venezia Giulia sono spazi di trasferimento tecnologico innovativo in cui sperimentare casi d’uso e rispondere alle domande “come lo faccio?”, “con chi lo faccio?”, “quanto mi costa?”.
Per capire come funzionano questi dimostratori abbiamo visitato in anteprima gli ambienti della Live demo di Padova ‘From Farm to Fork’, che diventerà operativa a inizio 2023. A fare gli onori di casa è stato Matteo Faggin, direttore generale del Competence center per l’Industria 4.0 Smact, che rappresenta un punto di riferimento su questi temi per le imprese del territorio (ma in realtà senza vincoli territoriali e quindi aperta a tutte le imprese a livello nazionale).
“Le nostre Live demo sono fabbriche scuola diffuse nei territori per permettere alle imprese di vedere e toccare con mano il potenziale della digital transformation”, spiega Faggin. La demo From Farm to Fork, che si trova a Padova nella zona del quartiere fieristico e delle università, è dedicata alle tecnologie digitali per l’agri-food.
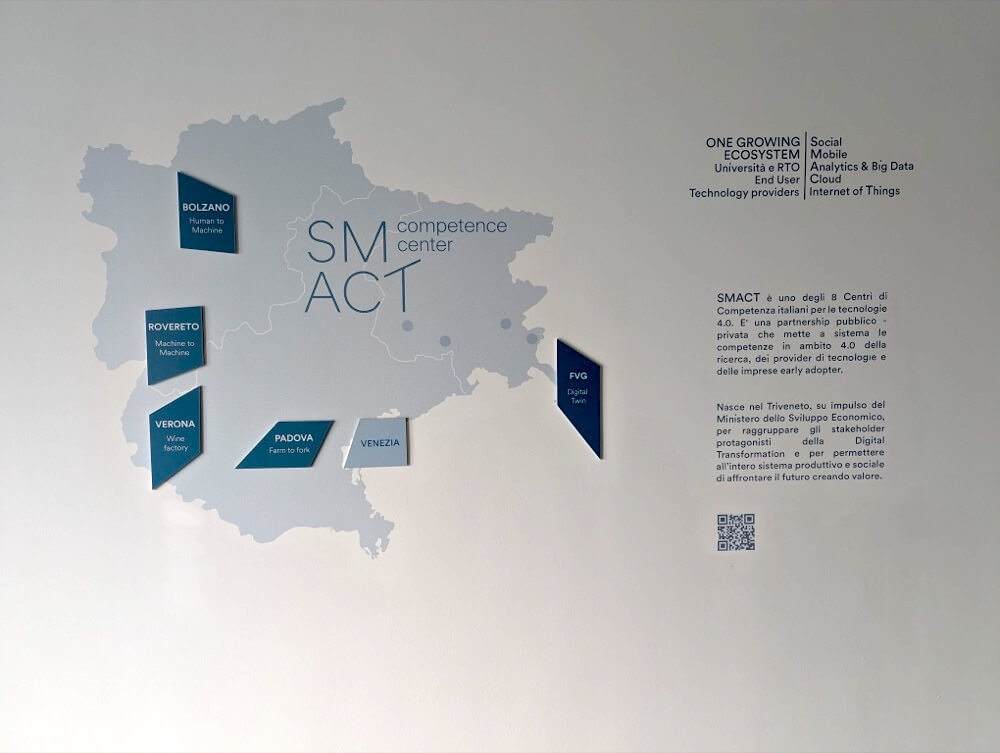
Con 3.000 metri quadri di struttura è il più grande dimostratore 4.0 d’Italia, dedicato alla filiera alimentare completa. È in pratica una fabbrica dimostrativa per il Food 4.0 composta da un birrificio artigianale, un panificio e una cucina industriale, che presto sarà dotata anche di una serra indoor 4.0 nella quale sperimentare tecnologie anche nel settore primario, per gestire e monitorare la produzione vegetale sostenibile.
In questa Live demo l’intero ciclo di produzione, dalla coltivazione in serra delle materie prime, alla produzione di pane, birra e piatti in vasocottura, viene interamente digitalizzato con sensori che raccolgono dati sulla gestione del clima, sul controllo dei parametri di produzione, sul monitoraggio dei consumi di acqua ed energia e per il controllo di qualità.
Tutti questi dati sono poi analizzati con l’intelligenza artificiale e trasmessi in cloud. Il tutto per arrivare a una gestione più efficiente e sostenibile della fabbrica alimentare 4.0.
La filosofia è di mettere a disposizione degli use case che permettano di “illuminare” le PMI anche di settori diversi, “perché abbiamo selezionato processi che si trovano anche in altri settori: dal trattamento fluidi alla cottura, dalle macchine rotative all’assemblaggio, alla logistica”, sottolinea il direttore generale di Smact.
Che osserva: “vedere come la digitalizzazione permette non solo di efficientare la produzione ma anche i prodotti, e toccare con mano le potenzialità dell’innovazione, aiuta a persuadere i piccoli imprenditori a intraprendere percorsi di innovazione e a formare il personale con esempi pratici anziché con lezioni teoriche”.
Indice degli argomenti
Sperimentare l’innovazione della filiera agroalimentare
Nella Live demo From Farm to Fork è possibile sperimentare una filiera agroalimentare che, partendo da una coltivazione agricola in serra indoor, porta alla produzione dei cibi sfruttando una materia prima di origine 100% naturale. La produzione delle tre linee sarà poi immessa nel mercato regionale e nazionale.
È una vera e propria Farm 4.0 realizzata anche con partner tecnici come Electrolux Professional, Gruppo Della Toffola, Sottoriva, Schneider Electric, ma con il coinvolgimento nella fase produttiva anche di realtà come Work Crossing (Forcellini Ristorazione), una cooperativa sociale che sviluppa la sua attività nel campo della ristorazione, impiegando categorie svantaggiate.
L’impianto di produzione della birra, progettato e fornito dal Gruppo Della Toffola, avrà una capacità produttiva annua di circa 25 mila litri di birra. Al suo interno “nuovi software, integrati con la rete e il software gestionale di Smact”, spiega Faggin, “per la gestione dei cicli di riscaldamento, di raffreddamento, di controllo tempi e di controllo della bollitura, per il controllo delle temperature di fermentazione e stoccaggio”.
Pane, birra e realtà aumentata, piatti pronti e AI
Realtà aumentata e supervisione da remoto consentono inoltre un costante controllo del funzionamento dell’impianto e di elaborazione dei numeri di processo: litri di birra prodotti, numero di bottiglie, tappi, etichette. Nell’impianto di produzione del pane, fornito da Sottoriva, vengono mostrate tutte le fasi di lavorazione a partire dalla miscela delle materie prime, il loro impasto, la successiva cottura e infine la parte di confezionamento e imballaggio.
Per ogni fase produttiva viene mostrato il beneficio tangibile che è possibile ottenere con l’impiego delle tecnologie di Industria 4.0: vengono mostrate ad esempio alcune possibili ottimizzazioni nel processo produttivo e la possibilità di risparmiare energia adattando il piano di produzione in funzione del ‘peso’ energetico del prodotto finito.
Innovare per produrre in modo più efficiente
Intelligenza artificiale, monitoraggio dei consumi, controllo di qualità ed efficienza di operatori e impianti sono al centro della linea di vasocottura: integra sistemi di intelligenza artificiale con videocamere per il riconoscimento di alimenti e temperature, sistemi intelligenti per la gestione del magazzino, lo stampaggio delle etichette, il controllo della qualità e dell’efficienza di operatori e impianti, una rete di informazione Smart grid per monitorare i profili di consumo e una dashboard per visualizzare i dati di sintesi.
Schneider Electric ha poi messo a disposizione una piattaforma IoT per la raccolta dati e una ‘control tower’ per le linee produttive: è la connessione di tutti gli asset della Live demo attraverso una piattaforma di raccolta dati e di messa a disposizione a livello edge, su interfacce cloud di rapido utilizzo.
Qui di seguito il video dell’intervista realizzata dal direttore di Innovation Post Franco Canna a Matteo Faggin