L’additive manufacturing sta riscontrando un crescente interesse nel mondo manifatturiero, affermandosi come uno dei temi più sulla cresta dell’onda. In questo articolo troverete tutte le informazioni di base per scoprire come sono fatti i nuovi macchinari, quali sono le tecnologie di processo e i materiali maggiormente interessanti.
Questo articolo è stato pubblicato sul numero di maggio 2018 della rivista Industry 4.0 Design Magazine (editore: Quine), la cui versione sfogliabile è disponibile a questo link.
di Enrico Annacondia, AITA – Associazione Italiana Tecnologie Additive*
Che cosa sono le tecnologie additive
Per ovviare ad una iniziale “vaghezza” del termine, è stata recentemente pubblicata una norma di validità mondiale, elaborata congiuntamente dagli enti normatori di vari Paesi. Secondo questo documento (denominato ISO/ASTM52921–1 “Standard Terminology for Additive Manufacturing-Coordinate Systems and Test Methodologies”), le tecnologie additive sono definite come “quei processi che aggregano materiali al fine di creare oggetti partendo dai loro modelli matematici tridimensionali, solitamente per sovrapposizione di layer e procedendo in maniera opposta a quanto avviene nei processi sottrattivi (o ad asportazione di truciolo)”.
Quale sinonimo, è spesso utilizzato, sui media e nel mondo dei maker e della personal manufacture, il termine “stampa 3D”. Anche per esso i normatori hanno individuato una definizione: “processi additivi che realizzano prodotti mediante la deposizione di materiale mediante una testa di stampa, ugelli od altre tecnologie di stampa)”. Invece, il termine “prototipazione rapida” è pressoché in disuso, in quanto le tecnologie additive sono sempre più spesso impiegate per creare parti funzionali (e non solo pezzi prototipali/dimostrativi).
Da ciò emerge un panorama applicativo in cui le tecnologie additive occupano un ruolo complementare a quello delle tradizionali, ossia le macchine utensili per asportazione/deformazione o, più in generale, i beni strumentali correlati a specifici materiali/prodotti. In tale panorama (identificabile come “manifattura additiva”), le tecnologie analizzate vanno a produrre modelli fisici, prototipi, componenti, attrezzature e prodotti di vario genere, impiegando una molteplicità di materiali: polimeri, metalli, ceramiche e materiali compositi (il ventaglio si sta rapidamente allargando, andando a comprendere, per esempio, tessuti biologici e composti alimentari quali la pasta o il cioccolato).
Sempre facendo riferimento alla norma sopracitata, questo può essere svolto, in linea di massima, secondo sette famiglie di processi:
- estrusione, dove il materiale (solitamente polimero), portato allo stato pastoso, è distribuito selettivamente mediante un orifizio; questo processo è tipicamente quello usato nelle macchine low-cost per la stampa 3D
- jetting, dove “goccioline” di materiale vengono spruzzate selettivamente per creare i layer (di polimeri, cera o metalli)
- binder jetting, dove un agente legante allo stato liquido viene spruzzato su uno strato di polvere (polimerica, ceramica, terre da fonderia, eccetera)
- sheet lamination che va a creare il manufatto mediante l’unione di fogli sagomati (solitamente di carta ma anche metallici)
- fotopolimerizzazione, basata sulla solidificazione selettiva di un polimero liquido mediante radiazioni elettromagnetiche (fornite da un laser o similare); in questa categoria rientra il noto processo di stereolitografia
- power bed fusion dove un flusso di energia opportunamente concentrato, fornito solitamente da laser o fasci di elettroni, va a fondere localmente uno strato di polvere (metallica o polimerica)
- direct energy deposition, dove un flusso di energia, fornito da un laser, fonde il materiale (tipicamente sotto forma di polvere metallica, convogliata nella zona di lavoro da un apposito erogatore) nel momento in cui esso viene depositato per costituire il pezzo.
È fondamentale notare che le tecnologie appena menzionate devono essere complementate da una serie di aspetti fondamentali per dare vita ad una reale filiera di manifattura additiva.
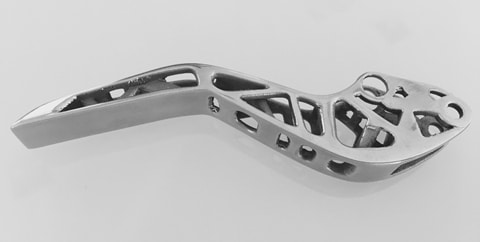
Indice degli argomenti
Tecniche di progettazione
Il processo di fabbricazione mediante processi additivi trae origine da un modello matematico 3D, teoricamente definibile per mezzo un qualsiasi CAD tridimensionale. Tuttavia:
- la possibilità di generare parti con geometrie virtualmente slegate dai vincoli di “design for manufacturing” consente di generare feature geometriche “atipiche” per i software tradizionali, come, ad esempio, strutture trabecolari, foam-like, a nido d’ape, eccetera, che ne’ la progettazione tradizionale ne’ la maggior parte degli strumenti di modellazione sono in grado di gestire efficientemente. Iniziano, tuttavia ad essere disponibili strumenti software che da un lato permettono di gestire queste problematiche e, dall’altro di gestire le fasi di progettazione integrando la definizione delle geometrie con la simulazione
- vanno rivisti i tradizionali approcci progettuali al fine di sfruttare i gradi di libertà offerti dalla nuova tecnologia, utilizzando approcci innovativi di progettazione che prevedono la generazione del pezzo a partire dalla missione cui è destinato (progettazione generativa) contrapponendosi all’approccio tradizionale che vede una geometria definita dal progettista e poi verificata con calcoli e prototipi (reali o virtuali)
- devono essere tenuti in conto i vincoli del processo additivo, con un vero e proprio “approccio di Design for Additive” che tenga in conto la necessità di sostenere parti “a sbalzo” durante la realizzazione, il ventaglio di materiali attualmente disponibili, l’impossibilità di realizzare fori troppo piccoli, ecc.
Post-processing
Le parti metalliche realizzate mediante tecnologie hanno livelli di finitura e tolleranze (geometriche e dimensionali) comparabili con quelli ottenibili mediante le tecniche di fonderia tradizionale. Questo richiede una rilavorazione alle macchine utensili che deve essere svolta considerando da un lato le caratteristiche dei materiali lavorati (spesso di difficile truciolabilità), dall’altro le geometrie non convenzionali permesse dalle tecnologie additive. Inoltre, in alcune applicazioni, è necessario svolgere post-trattamenti per migliorare le caratteristiche metallografiche e meccaniche del manufatto. Questa necessità è mitigata nella realizzazione di manufatti in polimero, dove spesso questa fase si riduce alla rimozione dei supporti
Caratterizzazione dei processi
È necessaria sia per attività “in-process”che garantiscano una costanza qualitativa dei manufatti generati (specie quando questi andranno a svolgere compiti “mission critical” come nel racing, nell’aerospaziale o nel biomedicale), sia per caratterizzare i materiali entranti ed uscenti dal processo
Generazione delle materie prime
Il costo, la disponibilità, la qualità e la numerosità di tipologie delle materie prime possono influenzare le performance tecnologiche ed economiche dei processi.
Aspetti di sicurezza
Sono legati a tipologie di macchine, materiali e processi spesso nettamente diversi da quelli tipicamente usati nel mondo del “manifatturiero tradizionale”. Questo aspetto è in corso di analisi da parte di un pool di esperti coordinati da INAIL e AITA – Associazione Italiana Tecnologie Additive, al fine di realizzare una linea di indirizzo che sarà pubblicata a breve.
Stato dell’arte in Italia e all’estero
Il settore delle tecnologie additive è un settore in rapidissima evoluzione. Diventa quindi estremamente difficile definire uno stato dell’arte consolidato, contrariamente a quanto può essere fatto in altri settori del manifatturiero.
L’unico aspetto in cui si può rilevare una certa “stabilità” è quello dei processi “base” impiegati dal settore delle tecnologie additive, ossia i sette visti in precedenza.
Al contrario, si possono rilevare variazioni pressoché quotidiane per quanto riguarda: applicazioni, sia a livello di settore industriale di sbocco, che di applicazione a prodotti esistenti (per svolgerne, ad esempio la mass customization) o creati ex-novo sfruttando le possibilità di design “illimitato” derivanti dalle tecnologie in oggetto; materiali lavorati, sia a livello di natura chimico fisica (nuovi materiali da elaborare), sia a livello morfologico (combinazione di materiali diversi per densità, colore, ecc. nello stesso manufatto); modelli di business che passano:
- per la produzione di macchinari, che vedono un rapidissimo succedersi di soluzioni innovative proposte da soggetti che spaziano dalle start up a multinazionali con fatturati elevatissimi
- per gli aspetti di utilizzo che vanno dall’uso privato/hobbistico (nel cosiddetto ambito dei maker o “artigiani digitali” che utilizzano normalmente software open-source e macchine low cost) a centri di servizio od aziende di produzione che integrano le tecnologie additive nella loro catena di generazione del valore al fine di migliorarne le performance a livello prodotto/processo/sistema
- per le applicazioni, anche qui estremamente varie e che spaziano dalla costruzione di oggetti per uso privato/ludico ad applicazioni ad altissima sofisticazione come quelle necessarie per le applicazioni spaziali o racing, dove diviene fondamentale la combinazione tra leggerezza e prestazione meccanica, a sua volta fortemente favorita dai minori vincoli progettuali in termini geometrici offerti. Va notato il progressivo indirizzamento dei player di settore verso:
- la realizzazione di macchine “grandi” (ossia con superfici di lavoro che tendono a superate 1×1 metri) al fine di realizzare batch numerosi di prodotti e/o pezzi di grosse dimensioni, spesso utilizzando soluzioni a più teste
- l’automazione e l’integrazione di processo, al fine di integrare le macchine additive nelle linee di produzione o di creare linee di produzione integrate basate sull’additivo. Ulteriore strada è quella di dar vita a macchine ibride additivo/sottrattive.
Focalizzandosi sul panorama italiano, il Belpaese si pone, insieme a Germania, Francia e USA, sopra la media degli altri paesi industrializzati, nonostante la relativa novità di queste tecnologie. Possiamo individuare alcuni aspetti peculiari del nostro Paese:
- nell’ambito dei centri di servizio, ben presenti nelle principali aree manifatturiere e in grado di svolgere attività di progettazione e realizzazione sia di prototipi, sia di manufatti
- a livello commerciale, dove filiali di produttori esteri e aziende commerciali forniscono una vastissima gamma di prodotti e soluzioni per l’impiego industriale delle tecnologie additive
- per quanto riguarda la produzione, i settori preminenti nell’ambito manifatturiero risultano essere quello della protesica (dove le tecnologie additive sono impiegate da aziende di primaria importanza su scala mondiale), il racing e l’aerospaziale.
Va infine notato che una spinta all’adozione delle tecnologie additive ben a sposarsi con le caratteristiche di flessibilità e customizzazione che caratterizzano le aziende manifatturiere (spesso PMI) italiane, a patto che si vada a creare l’opportuno tessuto culturale e di conoscenza. Questo aspetto è stato ulteriormente sottolineato dal “Piano Industria 4.0” del Governo Italiano che, nella misura dell’”iperammortamento” ha incluso tra i beni soggetti all’agevolazione fiscale (elencati nei ben noti “Allegato A” e “Allegato B”) l’intero set di beni necessari per implementare l’intera filiera di produzione additiva, spaziando dai software di progettazione fino a soluzioni di collaudo estremamente sofisticate quali la tomografia.
Perché orientarsi verso l’additive manufacturing
Le capacità “near net shape” (ossia quella di realizzare parti con forma anche molto vicina a quella finale) delle tecnologie additive non sono che la punta dell’iceberg tra i motivi che le stanno rendendo sempre più interessanti per il manifatturiero meccanico.
In realtà, vi sono anche altri motivi riconducibili a tematiche di natura gestionale e legate agli obiettivi delineati dal sopraccitato “Piano Industria 4.0” e più in generale della transizione del manifatturiero italiano verso la “manifattura digitale”. Tra questi possiamo individuare, in particolare, la richiesta di prodotti “green”, la mass customization e la “servitizzazione” (ossia la trasformazione del prodotto in servizio). Questi, infatti, sono tra i principali “input di mercato” che richiedono di pensare, progettare e costruire in maniera diversa i prodotti. Questi, in particolare, devono diventare leggeri, per ottenere maggior efficienza energetica, richiedendo, per contro, l’impiego di materiali più sofisticati di quelli utilizzati precedentemente (p.e. acciai speciali, titanio, compositi, ceramiche, materiali ibridi); e smart, integrando nuove funzioni grazie alle tecnologie informatiche che consentono di acquisire dati che ne migliorano le performance (specie ergonomiche ed energetiche) e l’integrazione, specie nell’ottica della servitizzazione.
Quanto sopra impone al manifatturiero meccanico di allontanarsi da alcuni suoi paradigmi tradizionali, per dar vita a un nuovo concetto di produzione (da molti identificato proprio con il “quattro-punto-zero”). Esso vede la “fusione” delle tecnologie di lavorazione (e delle relative macchine) con le tecnologie informatiche usate per effettuare, in maniera integrata, la progettazione, simulazione dei prodotti, dei processi e dei sistemi di produzione, nonché la conduzione, gestione e controllo di questi ultimi. Ciò al fine di adattare il più rapidamente e flessibilmente possibile il sistema manifatturiero a nuove esigenze produttive, a loro volta legate a nuove e, normalmente, più sofisticate richieste del mercato.
Se, da un lato, i produttori sono stati capaci di inserire nelle macchine utensili moderne le funzioni e le tecnologie necessarie per soddisfare numerosissime esigenze del nuovo paradigma “4.0”, dall’altro sono emerse nuove necessità produttive che vanno affrontate con tecnologie nuove.
Tra queste nuove necessità emerge quella di slegarsi dalle classiche regole del “design for manufacturing”, a loro volta collegate a doppio filo ai classici processi delle tecnologie meccaniche. Inoltre, le necessità di accorciare la catena produttiva per realizzare prototipi funzionali o, meglio, prodotti personalizzati in piccole o piccolissime serie (e/o di lavorare materiali inconsueti) contribuiscono alla domanda di nuovi processi produttivi. Con le tecnologie additive è anche possibile apportare sensibili cambiamenti alla sequenza produttiva del prodotto, in termini di
- riduzione di attrezzature ed eliminazioni di parte del ciclo produttivo, con impatto su flessibilità di processo e time to market;
- riduzione o eliminazione di fasi di assemblaggio, dando per esempio origine a parti complesse senza necessità di saldature o incollaggi, oppure a veri e propri cinematismi;
- possibilità di creare feature geometriche molto complesse e di difficile/impossibile creazione con altre tecnologie;
- possibilità di lavorare materiali di difficile lavorabilità (leghe per alta temperatura, compositi metalloceramici) o di natura “inconsueta” per il manifatturiero (come, in prospettiva, materiali biologici “viventi” come cellule e tessuti);
- riduzione di scarti e sfridi di lavorazione;
- migliorare altri processi industriali permettendo la realizzazione di attrezzature più efficienti (p.e. stampi “conformant cooling”).
Per ottenere questi risultati, il settore della manifattura additiva mette e metterà a disposizione delle aziende che intendono evolvere verso il “digital manufacturing” soluzioni riguardanti:
1. macchine/processi
- Dimensioni delle macchine, al fine di poter produrre parti di maggior dimensione o batch di pezzi più numerosi (con riduzione del costo unitario), come già menzionato precedentemente nell’articolo
- flessibilità a livello di materiali lavorati, sia per quanto riguarda le tipologie, sia per quanto riguarda i tempi di set-up macchine (al fine di realizzare prodotti di materiali diversi con meno tempi morti e/o realizzare elementi multi-materiale)
- controllo di processo, specie per la produzione di parti non prototipali da impiegare in applicazioni ad alte prestazioni (aerospace, racing, biomedicale) e per garantire la qualità e costanza delle lavorazioni
- valutando l’integrazione con altri processi produttivi a livello di macchina (p.e. macchine ibride) e a livello di sistema (p.e. catene produttive che integrano a livello di produzione “mass-customizzata” i processi additivi).
2. materiali
- aumentandone la disponibilità, per diminuirne i costi e favorire la competitività delle nuove soluzioni basate sulle tecnologie additive. Va inoltre considerata l’opportunità competitiva per il nostro Paese legata all’aumento dei produttori di materie prime, attualmente molto rari sul suolo nazionale
- relativamente alle metodologie di produzione, specie per le polveri metalliche, con processi più efficienti (a livello di produttività e resa energetica) rispetto agli attuali e in grado di garantire qualità e prestazioni
- per le tipologie di materiali lavorabili, estendendo la gamma di quelli già manipolabili con le tecnologie additive (metalli, polimeri, compositi, ceramiche) sia per quelli “in prospettiva” (generi commestibili, elementi biologici)
3. prodotto
- Ripensando prodotti già esistenti sul mercato in funzione della realizzabilità con processi additivi, al fine di alleggerirli, aumentarne le prestazioni, renderli più sostenibili, realizzarli con materiali o geometrie nuove e ottimizzate, sia per performance che per design (aspetto molto utile per quanto riguarda il legame con il “made in Italy e le sue implicazioni industriali)
- realizzando nuove generazioni di prodotto che si basano sulle caratteristiche di “free forming” (derivante dalla progettazione generativa) e di “near net shape” (nonché sulla possibilità di lavorare materiali difficili o inconsueti)
- realizzando prodotti ibridi che integrano parti realizzate “in additivo” con altre prodotte con tecnologie differenti/materiali diversi; questo al fine di economizzarne o velocizzarne la produzione o per portare all’integrazione di funzioni nel prodotto (p.e. sensoristica o altre funzioni di natura ICT, energy harvesting, caratteristiche estetiche personalizzate)
4. gestionale
- sfruttando le potenzialità a livello di mass customization e di personalizzazione
- per creare nuovi modelli di business per le PMI italiane, grazie alla servitizzazione (passando, per esempio, da subfornitori a centri di servizio che integrano produzione, progettazione e design)
- creando nuovi modelli di sicurezza informatica e tutela della proprietà intellettuale che preservino dalle contraffazioni.
Non va, infine, dimenticato che le tecnologie additive sono per natura “digital”. Infatti, l’intera generazione del prodotto (almeno fino all’uscita della macchina additiva) è totalmente gestita in maniera “informatizzata”, in quanto la catena di design/simulazione, modellizzazione, generazione dei part program e produzione del pezzo in additive avviene senza “rottura del media” informatico (non richiede, cioè, il passaggio di informazione dal computer alla carta e viceversa).
Conclusioni
Le tecnologie additive, nell’ambito dei metalli, delle materie plastiche e di numerosi altri materiali (quali le ceramiche) stanno prepotentemente uscendo dalla dimensione della prototipazione e della piccola serie, andandosi ad affiancare alle macchine utensili in produzioni sempre più caratterizzate da una dimensione industriale. Tuttavia, non è pensabile affrontare, da parte degli utilizzatori, la transizione verso la produzione additiva in una ottica di mera sostituzione. Infatti, allo stato attuale:
- le macchine additive e quelle sottrattive sono nella maggior parte delle applicazioni, specie per il metallo, complementari
- i prodotti vanno riprogettati in ottica di design for additive manufacturing, tenendo conto della limitata gamma (se comparata con la manifattura tradizionale)
- la catena di generazione del valore e, conseguentemente, l’impostazione organizzativa e gestionale delle aziende deve essere ridisegnata, spesso andando ad adottare in maniera molto sofisticata, i paradigmi della cosiddetta “Impresa 4.0/digital factory”
- vanno attentamente considerate le modalità di collaudo e qualificazione dei prodotti e dei processi, tenendo particolarmente in conto che il materiale “finale” del pezzo viene letteralmente creato durante il processo additivo
- il ventaglio di normative in grado di descrivere i vari aspetti della filiera additiva è ancora largamente incompleto
- i modelli di costo da adottare nella filiera di prodotto/processo/sistema possono differire pesantemente da quelli adottati per la manifattura tradizionale, con pssibili impatti inattesi sulla redditività aziendale
- vi è ancora una carenza di figure professionali adeguatamente “skillate”, sia a livello operativo che manageriale, in grado di gestire le sfaccettature di questa innovativa tecnologia .
- tuttavia, il rapido sviluppo del settore, unito al grande interesse di numerosi settori industriali, porterà a risolvere, in un ottica di medio e breve periodo,
Il settore italiano dell’additivo, che rappresenta una delle eccellenze a livello mondiale grazie al coordinamento di AITA – Associazione Italiana Tecnologie Additive, non sta sicuramente assistendo passivamente allo sviluppo del settore ma ne è parte assolutamente attiva. Inoltre, l’associazione sta promuovendo una iniziativa, denominata “convegni itineranti” che, con eventi in varie città italiane, permetterà alle aziende interessate all’adozione delle tecnologie additive di confrontarsi con i principali player operanti sulle varie componenti della filiera produttiva.
Sul sito associativo www.aita3d.it e su queste pagine sarà data informazione su date, luoghi e programmi. Inoltre, lo stand associativo di AITA presso la fiera 31.BIMU (www.bimu.it) ospiterà una edizione speciale dell’evento, dove il mondo della macchina utensile potrà identificare le opportunità offerte sinergicamente da questo nuovo mondo di produrre.
Che cos’è AITA
AITA – Associazione Italiana Tecnologie Additive è un’associazione culturale che intende rappresentare gli interessi dei player del settore (aziende produttrici ed utilizzatrici, fornitori di tecnologie abilitanti, centri di servizio, università e centri di ricerca, ecc.), favorendone il dialogo con enti, istituzioni ed altre associazioni industriali, al fine di fare conoscere e sviluppare le tecnologie additive e la stampa 3D.
AITA – Associazione Italiana Tecnologie Additive nasce dall’iniziativa dei suoi soci fondatori, supportata e sostenuta operativamente da UCIMU-SISTEMI PER PRODURRE, che ha messo a disposizione dell’iniziativa le risorse necessarie e la sede associativa.
La missione associativa intende aggregare tutti gli stakeholder che «gravitano» attorno alle Tecnologie Additive: aziende legate alle Tecnologie Additive ed alle sue macchine/utilizzi industriali, produttori, importatori, utilizzatori diretti, centri servizi, ecc…, aziende che si correlano con il settore delle Tecnologie Additive ma non ne fanno direttamente parte (end-user, fornitori di tecnologie ICT, ecc…), centri di ricerca, università, enti pubblici e governativi che operano su aspetti correlati (RTDI, finanziamenti, …). L’associazione inoltre intende svolgere azioni trasversali e raccogliere informazioni condivise, dare voce concreta ad un settore emergente, creare una «immagine» delle Tecnologie Additive coerente con il loro ruolo nel manifatturiero, svolgere attività legate alla ricerca e innovazione, creare vantaggio competitivo, favorire le applicazioni industriali delle Tecnologie Additive e il loro collegamento con gli altri processi del manifatturiero meccanico.
In linea di massima le attività di AITA si articolano su: standardizzazione, comunicazione e promozione, formazione, Ricerca e Sviluppo, eventi, mostre e fiere, ulteriori temi indicati dal Consiglio Direttivo.
Ad oggi, AITA conta 112 soci.
Per ulteriori informazioni: www.aita3d.it , info@aita3d.it