Contributo di Riccardo Francazi, R&D Manager di Servotecnica – Gestione della comunicazione dati a livello di ingressi e uscite nei macchinari automatici. È questa la funzione di IO-Link. È economico, semplice ed efficiente.
Fatta questa premessa, i lettori vorranno saperne di più. La documentazione riguardante l’impiego di IO-Link per la gestione del traffico di ingressi/uscite è ampia, ma le informazioni sul suo uso nel campo del motion control sono scarse. Pur non sottovalutandone i limiti in questo campo, in questo articolo esaminiamo le applicazioni di IO-Link proprio nel motion control.
Basta chiedere quali sono le caratteristiche principali di IO-Link a un utilizzatore per sentirsi immancabilmente rispondere che è una soluzione semplice, solida ed economica per tutto il ciclo di vita della macchina, che è facile da integrare, installare, mettere in esercizio e anche da utilizzare, oltre al fatto che facilita la manutenzione… Per inciso, IO-Link è anche una soluzione ottimale per applicazioni di motion control semplici, ed è proprio questo l’aspetto su cui vogliamo concentrare qui la nostra attenzione. Ma, prima di tutto, vediamo cos’è IO-Link.
Indice degli argomenti
NO bus di campo, universale, predisposto per Industry 4.0…
In effetti, IO-Link è uno standard (IEC 61131-9) definito dall’organizzazione internazionale IEC. Lo standard definisce le specifiche di un’interfaccia SDCI – Single-drop Digital Communication Interface – per piccoli sensori e attuatori. A prescindere dal controller (e dal protocollo – bus di campo – di comunicazione dati) utilizzato per l’automazione del sistema, la “parte 9” dello standard “IEC 61131” definisce le specifiche di una tecnologia SDCI unica e universale, adatta per applicazioni che impiegano piccoli sensori e attuatori (ampiamente usati sui macchinari).
Sebbene l’organizzazione IO-Link sia uno dei membri del consorzio Profinet, gli utilizzatori non devono necessariamente adattare i loro sistemi di sensori/attuatori (connettori, cavi, dispositivi hardware e software) ad alcun protocollo di bus di campo specifico. Come si dice spesso, “IO-Link è una soluzione universale interprotocollo” e si adatta a qualsiasi architettura basata su Modbus, PROFIBUS, EtherNet/IP, AS-I, ecc.
L’obiettivo è semplice e chiaro: estendere le tradizionali interfacce digitali di ingresso e uscita nella direzione di una comunicazione punto a punto (indipendentemente dal bus di campo adottato a livello di PLC).
Nel campo, questa tecnologia supporta la trasmissione bidirezionale di dati di processo, manutenzione ed eventi fino al dispositivo misuratore che opera nel punto più interno della macchina e includendo tutti i sensori e gli attuatori. Sia i master che i dispositivi adottano un protocollo specificato conformemente al modello di riferimento ISO/OSI (livello fisico, livello di collegamento dati e livello di applicazione). IO-Link consente inoltre il trasferimento di dati di controllo e parametri fino ai dispositivi, oltre all’invio dei dati di processo e delle informazioni di diagnostica al sistema di automazione dai singoli dispositivi.
Dal punto di vista fisico, IO-Link si basa su una tecnologia semplice, solida e ben collaudata: il classico collegamento a tre fili usato per i comuni sensori e attuatori, senza alcun requisito aggiuntivo in termini di cablaggio. Citando le parole dei suoi promotori, si tratta di “un’ulteriore evoluzione della tecnologia di collegamento esistente e ben collaudata di sensori e attuatori”. E non prevede la necessità di interfacce e sistemi di comunicazione basati su collegamenti multipunto o multidrop. Detto questo, IO-Link viene essenzialmente utilizzato per l’automazione di fabbrica e trova ampio impiego con sensori ed attuatori semplici, nelle applicazioni che includono microcontroller di piccole dimensioni ed economici.
In altre parole, uno dei vantaggi principali di questo standard sta nel fatto che il livello di sensori e attuatori (ingressi e uscite) può rimanere inalterato, indipendentemente dal controller di livello superiore della macchina e/o dal controller di tutto il sistema di automazione. Ciò consente di ridurre i tempi di progettazione e ingegnerizzazione, di diminuire il numero di ricambi e componenti per riparazioni da conservare a magazzino, di ridurre i “grattacapi” e di garantire maggiore tranquillità. Di fatto, questo standard è universale e si adatta a svariate applicazioni.
Come dicono alcuni utilizzatori: “IO-Link sta rivoluzionando le comunicazioni a livello di campo”. Rende disponibili i dati da tutti i livelli di macchina e di tutto il sistema, perfettamente in linea con le strategie di Industry 4.0. Essendo predisposto per Industry 4.0, questo standard offre oggi – e lo farà sicuramente in futuro – le potenzialità necessarie per implementare funzioni di macchina migliorate e persino completamente nuove. Nel futuro di IO-Link sono già previste tecnologie di produzione migliori e più economiche. Più concretamente, questo standard permette e garantisce investimenti a lungo termine.
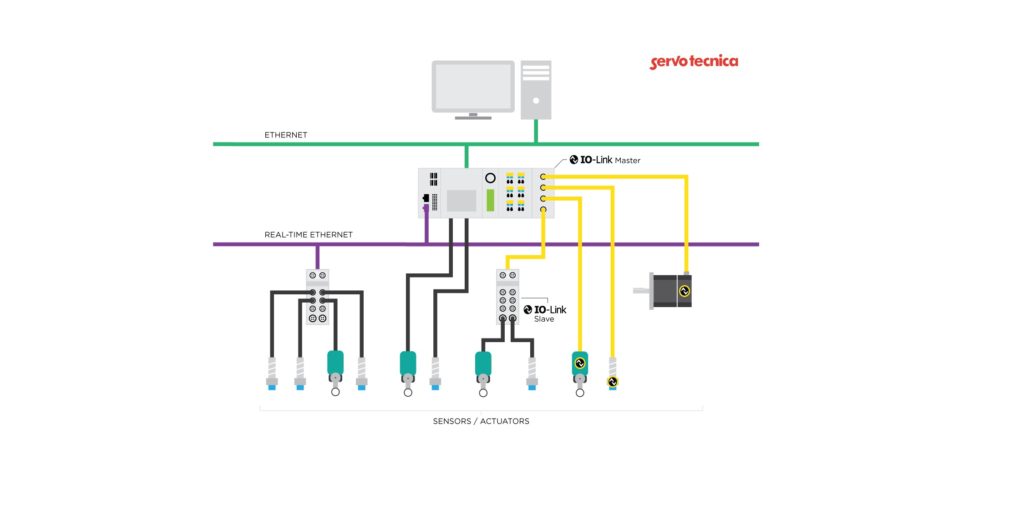
Economico, facile da integrare, implementare, usare, diagnosticare e manutenere…
Il rapporto costi-benefici di IO-Link è positivo. Ancora prima di arrivare sul campo come soluzione fisica e concreta, aiuta a ridurre i tempi di ingegnerizzazione tagliando i tempi degli studi progettuali e della fase di preparazione alla messa in esercizio. E quando “scende in campo”, la messa in esercizio è più rapida. Come anticipato, IO-Link utilizza cavi standard e contribuisce anche a ridurre le scorte a magazzino dei ricambi grazie a dispositivi multifunzione intelligenti.
Oltre a ciò, IO-Link semplifica la diagnostica della rete di sensori e attuatori e anche l’organizzazione degli interventi di manutenzione. Funzionalità di diagnostica ampliate permettono infatti di eseguire la diagnosi in remoto fino al livello dei dispositivi sul campo, per rilevare rotture di cavi e diagnosticare dispositivi specifici. Grazie alla sua semplicità e solidità, alla facilità e rapidità di manutenzione e riparazione, IO-Link contribuisce ad aumentare i tempi di attività dei sistemi di macchinari. Senza scendere troppo nei dettagli su questo aspetto, ciascun dispositivo sul campo viene descritto tramite un file IODD (IO Device Description), che contiene informazioni quali il produttore del dispositivo, il numero del modello e quello di serie e il tipo di dispositivo, oltre ai parametri correlati all’applicazione. I valori di questi parametri possono essere modificati da remoto (tramite il master), in modo che la macchina possa essere adattata da remoto e online per il lotto di produzione successivo. Analogamente, sebbene i parametri di un collegamento risiedano nel master (hardware), possono essere ripristinati, regolati e modificati dinamicamente durante il processo di produzione. E se un’unità master deve essere sostituita per una qualsiasi ragione, basta eseguire solo la pre-configurazione (in ufficio o in laboratorio) e la sostituzione (sul campo). In questi casi, si tratta solo di una “sostituzione meccanica” da effettuare nella centralina della macchina. Grandioso, vero? E anche facile.
In sintesi, IO-Link è orientato all’automazione di fabbrica e ai macchinari. I concetti di macchina innovativi su cui si basa IO-Link assicurano un’installazione più semplice. Standardizza interfacce e sistemi di cablaggio (paralleli, analogici, digitali) in un’unica tipologia, e i concetti di macchina modulare sono intrinsecamente supportati. I moduli delle funzioni e il supporto fornito dagli strumenti consentono un’impostazione altamente automatizzata dei parametri. Progettazione, messa in esercizio e manutenzione risultano quindi più rapide e semplici.
Tutte queste semplificazioni portano, naturalmente, a una riduzione della documentazione e dei costi di formazione.
IO-Link e il Motion Control
Per le comuni applicazioni I/O sono disponibili molte informazioni. Molte di meno, però, sono quelle che riguardano le applicazioni di motion control. Beh, secondo il punto di vista degli autori di documentazione tecnica, il motion control suscita grande interesse in termini di applicazioni di motion control avanzato che devono gestire velocità elevate e/o posizionamenti ciclici, o ancora applicazioni che richiedono solitamente numerosi calcoli di interpolazione e/o applicazioni che utilizzano ingranaggi e/o camme elettrici.
D’altro canto, però, sebbene i produttori e i fornitori di sistemi di motion control possano offrire tali applicazioni complesse, molti utilizzatori sono semplicemente alla ricerca di applicazioni facili da progettare. E, dato che IO-Link supporta solo cicli di automazione piuttosto lenti, può rispondere perfettamente a questa esigenza.
In tali applicazioni, i sensori misurano e controllano valori e parametri di processo come angoli, distanze, frequenze e impulsi, livelli, posizioni, pressioni, conteggi di rotazione o scorrimento, velocità lineari o di rotazione, temperature, ecc.
Intervalli e soglie di misurazione devono essere impostati in modo variabile in funzione di vari lotti di produzione. Se prima queste variazioni venivano in genere eseguite manualmente (con il rischio di dover gestire errori umani e correzioni), IO-Link consente di impostarle da remoto. Il master IO-Link è in grado di riconoscere sensori, attuatori e display connessi. Prima dell’avvio della produzione, controlla i parametri di configurazione di tutti i dispositivi. Sebbene non siano complesse in termini di velocità o interpolazioni, molte applicazioni di motion control utilizzano numerosi parametri. E in questo caso l’impostazione dinamica dell’applicazione costituisce un vero e proprio vantaggio.
Il mercato globale dei macchinari è messo a dura prova. La competizione è serrata! In questo contesto la giuria è composta da… gli utilizzatori! E gli utilizzatori guardano a queste soluzioni per l’affidabilità dei macchinari e si aspettano che le macchine possano ripagare rapidamente l’investimento.