Il periodo forzato di lock-down e la ripresa, con la necessità di lavorare adottando tutte le precauzioni necessarie ad assicurare una convivenza sicura con il virus, a tutela dei lavoratori e della continuità di business, hanno mostrato come le realtà produttive più avanti nel processo di smart manufacturing, abbiano potuto adeguarsi con maggiore velocità e flessibilità alle nuove necessità. Solo nei prossimi anni si potranno effettivamente analizzare e confrontare i dati per correlare prestazioni e risultati con il livello di maturità in ambito smart manufacturing e industria 4.0. Nel frattempo, possiamo ribadire alcuni concetti fondamentali che trovano riscontri positivi da chi li abbia fatti suoi.
Indice degli argomenti
Le parole chiave dello smart manufacturing
Le parole chiave sono: flessibilità, condivisione, collaborazione.
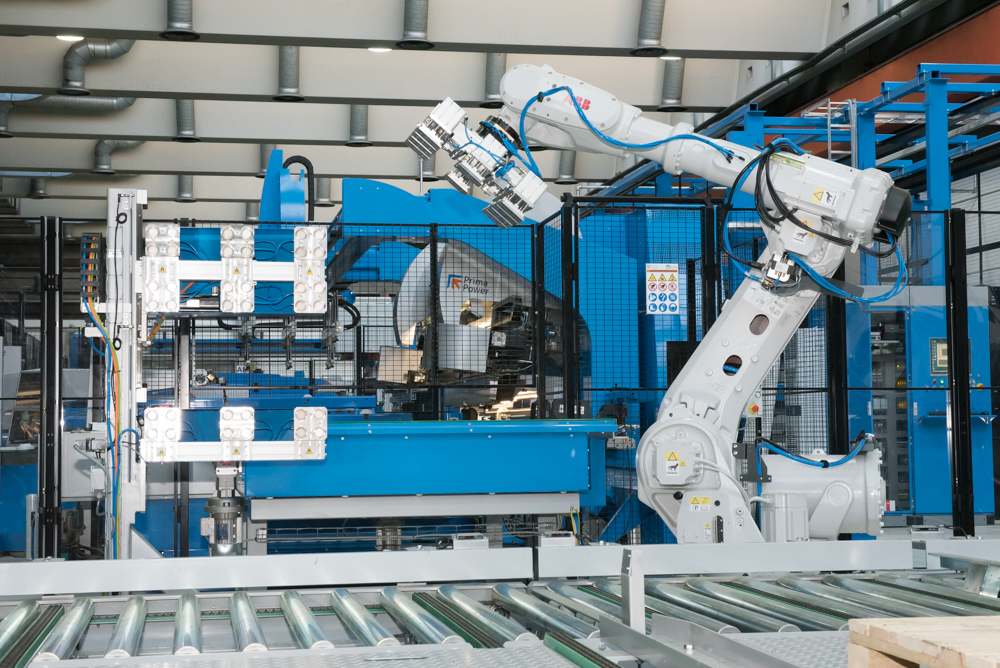
Stabilimento ABB Dalmine, produzione lamiere
Flessibilità
Il repentino e drammatico cambio di abitudini che il mercato consumer ha avuto negli ultimi anni, innescato e supportato dalle nuove tecnologie e dai servizi correlati (si pensi ad esempio a smartphone, social, siti di vendita on-line), hanno avuto un effetto dirompente su tutta la filiera a monte, arrivando a scuotere l’industria manufatturiera.
I cicli a cui si era abituati, tipici per ciascuna filiera, settore o cluster di prodotti, sono stati stravolti o hanno comunque risentito dei cambiamenti e la novità in molti settori è rappresentata dalla necessità di garantire ampi gradi di flessibilità, maggiori di quanto fosse richiesto nel passato.
La flessibilità si declina in differenti caratteristiche e tipicamente coinvolge la capacità produttiva. Le principali richieste di modifica vertono nelle quantità per unità di tempo e nel cosa si produce, chiedendo capacità di differenziazione e/o personalizzazione. Naturalmente, esistono altre variabili che rendono ancor più complesso il quadro che sta dietro alle richieste di modifica. Generalizzando, il tutto si riconduce alla necessità di adottare linee di produzione e filiere che alimentano la produzione con gradi di flessibilità tali da sbloccare e rendere fattibili le modifiche richieste, compatibilmente con i tempi dettati dal mercato.
Per gestire la flessibilità, necessariamente si deve mette in discussione la relazione con i due ambiti a monte e a valle della produzione e questo implica affrontare la questione della condivisione.
Condivisione
La condivisione è alla base della flessibilità produttiva. Ma cosa condividere e con chi? La risposta banale è: tutta l’informazione utile alla controparte per i suoi scopi e per contribuire ai nostri obiettivi.
Nel caso del cliente, le informazioni tipicamente riguardano quanto si sta producendo e sarà oggetto di fornitura, nel caso di fornitori e partner, quanto sarà richiesto per portare a termine una fase produttiva.
Con questa generalizzazione e semplificazione si potrebbe obiettare che non è nulla di nuovo in linea di principio. La prospettiva assume differenti connotati se condividere implica l’aprire i propri sistemi e macchine di produzione per scambiare con l’esterno informazioni, ovvero essere connessi. Esprimendoci in modo complementare, non disporre di macchine e sistemi di produzione connessi è di fatto una forte preclusione alla condivisione.
Disponendo di flessibilità e adottando un approccio aperto nei confronti della condivisione si accede a potenziali nuovi livelli di collaborazione con quanto è all’esterno della fabbrica.
Collaborazione
La collaborazione è nella natura umana e qualsiasi contratto regolamenta di fatto una collaborazione, definendone i confini e gli ambiti entro cui muoversi, in una visione semplificata del concetto. La trasformazione digitale consente di dare nuovi connotati alla collaborazione. Di fatto ciascuna persona o oggetto connesso alla rete amplia i propri confini fisici, circondandosi di una aureola digitale. L’aureola digitale consente la condivisione ed è il fattore abilitante per nuove modalità di collaborazione, ovvero la creazione di ecosistemi che sfruttano al meglio il connubio flessibilità-condivisione-collaborazione.
L’aureola digitale obbliga a uscire dai propri confini, rispetto ai quali tipicamente ci si confrontava e rispetto ai quali si operava, richiedendo di gestire in modo opportuno nuove questioni riguardo la sicurezza che, usando terminologia inglese, è da intendersi sia come security che come safety.
Non entriamo qui nel merito della questione sicurezza, se non liquidare il tutto con una battuta: gli eventi legati al Covid-19 hanno forzato anche i più restii a rivalutare le riserve che avevano riguardo a vari temi tecnologici (per esempio il cloud), proprio portando a giustificazione questioni di sicurezza. È altresì chiaro che il ripensamento richieda comunque di affrontare la questione in modo professionale, senza tralasciare e trascurare gli aspetti legati alla sicurezza.
Concretizziamo il ragionamento con alcuni esempi.
Il business e il cliente
Secondo il ragionamento fin qui seguito, smart manufacturing implica dominare e disporre di flessibilità-condivisione-collaborazione, e nella nuova architettura che si viene a creare al centro c’è il business, ovvero il cliente.
Volutamente non mi limito a citare solo il cliente, come solitamente viene fatto, ma comprendendo anche il business. Questo perché dove il business è rimasto immutato è chiaro chi sia il cliente e che questo debba occupare il ruolo centrale del nuovo assetto e dei processi. Però ci sono anche contesti in cui il business è mutato o è in una fase di mutamento; in questi casi il “cliente” potrebbe essere più evanescente come realtà, almeno in questa fase. Resta inteso che in entrambi i casi, una focalizzazione sul business è fondamentale, come è fondamentale la disponibilità a ridiscuterlo criticamente e continuamente, in termini di business model, ma anche di cosa si voglia fare: sono ormai diffusi casi in cui aziende, che grazie alla flessibilità produttiva o aver approcciato nuovi mercati attraverso gli ecosistemi costituiti, abbiano diversificato il loro business o intrapreso nuove strade.
Mettere al centro il cliente implica modificare il tipo di coinvolgimento e di relazione, arrivando a livelli di confidenzialità e condivisione che sono inusuali nei rapporti passati. Spesso questo ha ripercussioni sulla attività di sviluppo dei prodotti e delle soluzioni, arrivando per esempio: a mettere in piedi una attività congiunta di R&D, intraprendere azioni di ottimizzazione dei prodotti e servizi erogati dal cliente, sviluppare un approccio congiunto/coordinato sul mercato. In molti casi, si rimane nel settore di mercato usualmente presidiato, in altri si esplora la possibilità di espandersi in nuovi settori. Questo confronto porta anche alla condivisione di informazioni legate ai costi, visto dal lato del fornitore, e alle prestazioni sul mercato, visto dal lato del cliente.
Per la natura delle questioni trattate, tipicamente queste relazioni sono soggette ad accordi di riservatezza. Pertanto, i dettagli e i risultati non sono divulgabili e di dominio pubblico e questo è ancor più vero ove si vogliano creare nuovi servizi e opportunità di business sul mercato.
Smart manufacturing, la filiera a monte
Se il business e il cliente sono centrali nella nuova architettura di produzione, specularmente la filiera a monte, che alimenta il processo produttivo, dovrebbe riproporre lo stesso approccio. In questa prospettiva la prima considerazione banale è che chi prima era fornitore, ora diventa il cliente che interagisce con i propri fornitori.
Considerando il panorama manufatturiero italiano caratterizzato da molte aziende di piccola media grandezza, che hanno fatto della loro competenza, velocità di esecuzione e qualità di quanto producono i loro punti di forza, quanto sopra è di per se una sfida e una opportunità.
In alcuni settori alcune aziende fornitrici si sono già confrontate con richieste di adeguamento dei loro processi e i meccanismi di interazione con i clienti, per rispondere a questioni di tracciabilità, riduzione delle scorte a magazzino, automazione e processamento degli ordini attraverso la condivisione della pianificazione degli ordini di lavorazione, e altro.
Questa volta però l’effetto della richiesta è molto più profondo e diventa l’occasione per gettare solide basi di sviluppo, incrementando aspetti quali la competitività, la produttività, la qualità, il posizionamento dell’azienda sul mercato.
Non tutte le aziende sono però in grado di affrontare e gestire questa sfida da sole. Un beneficio e un’agevolazione sia ha se si è parte di un ecosistema dove è l’insieme a muoversi in questa direzione e si creano le condizioni per gestire la transizione e il percorso da intraprendere insieme ad altri, con chi possa anche guidare i passi onde evitare errori o inutili perdite di tempo.
Essere e agire da Lighthouse Plant
Per andare ancora più in concreto su quanto fin qui illustrato, portiamo ad esempio il sito produttivo ABB di Dalmine. Lo stabilimento produce interruttori, sezionatori e quadri elettrici di media tensione, con un turn over di circa 350 milioni di euro all’anno e 860 dipendenti. Il sito si caratterizza per l’indotto significativo e per essere un riferimento all’interno del Gruppo ABB. Qui si sperimentano nuove soluzioni che sono poi adottate all’interno del Gruppo o diventano il dimostratore dell’efficacia del prodotto o la soluzione sul mercato. Il percorso intrapreso a Dalmine parte con una ostinata perseveranza nell’adottare l’approccio lean, puntando a una sempre migliore sincronizzazione della fabbrica con le richieste del mercato, eliminando gli sprechi.
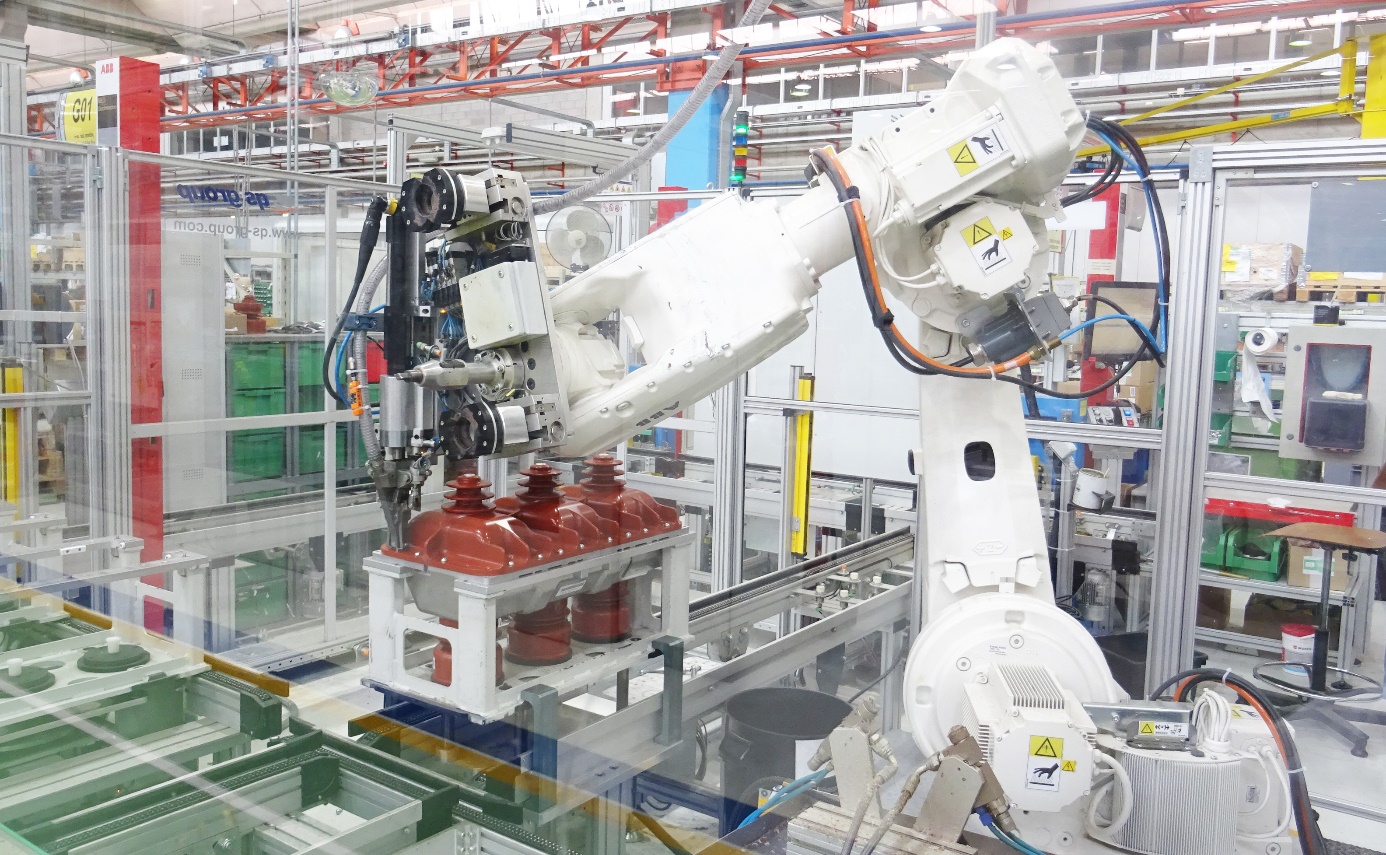
Stabilimento ABB Dalmine, produzione sezionatori
Questa sua storia lo ha reso naturalmente un candidato ideale a divenire un Lighthous Plant, ovvero una fabbrica che aprendosi possa illustrare come i benefici e l’efficacia dello smart manufacturing e dell’industria 4.0, rivolgendosi non solo alle aziende della sua filiera, ma a tutti.
Lo stabilimento di Dalmine costituisce, insieme alle fabbriche di Frosinone e Santa Palomba, uno dei tre Lighthouse Plant ABB selezionati dal Cluster Fabbrica Intelligente per conto del ministero dello Sviluppo Economico[1]: uno dei modelli di riferimento, da seguire per le aziende che puntano alla digital transformation, secondo la filosofia Industry 4.0.
La roadmap di Dalmine per lo smart manufacturing e industria 4.0, che incrocia i problemi da risolvere con le tecnologie utili per farlo, include tra le principali aree oggetto di sviluppo: la gestione dei flussi, i cobot, i big data e analytics (per la manutenzione predittiva e per il controllo di qualità), i robot, l’additive manufacturing, l’IoT, la realtà aumentata, la realtà virtuale, la sostenibilità, l’economia circolare… il tutto condito con l’intelligenza artificiale: la battuta per evidenziare un elemento che sempre più sottende a quanto stiamo facendo e faremo, nelle nostre fabbriche, ma anche nelle nostre vite.
Il Covid-19 ha dato maggiore ragioni per percorre la strada intrapresa: si pensi alla rivisitazione della supply-chain e delle linee di produzione per soluzioni che risultino “anti Covid-19”, ovvero in grado di mostrare resilienza rispetto a quanto possa accadere nel mondo. Come nota su questo punto, da condividere come la fabbrica di Dalmine non si sia mai fermata: questo grazie alla flessibilità e il lavoro intrapreso in ottica smart manufacturing. Naturalmente, l’eccezionalità di quanto vissuto è stato altresì fonte di elementi, utili per i prossimi passi, sempre nell’ottica di incrementare le prestazioni e la resilienza della fabbrica, nonché a sempre maggior tutela dei lavoratori.
Uno dei temi affrontati causa Covid-19 è stato quello dello smart working in ambito industria, ovvero la gestione remota dei processi produttivi. L’esperienza di Dalmine mostra come la presenza di un sistema MOM – Manufacturing Operations System, evoluzione del più noto sistema MES – Manufacturing Execution System, abbia in tal senso facilitato il compito.
Se il MES gestisce il processo produttivo connettendo le linee di produzione e le loro macchine, il MOM è il connettore tra la produzione e il gestionale aziendale, arrivando a fornire indicazioni in ambiti quali la qualità, la manutenzione, l’inventario, la pianificazione, la tracciabilità, la gestione del magazzino e la gestione delle giacenze. Disporre di tali spaccati di fabbrica da remoto ha consentito di limitare la presenza fisica allo stretto indispensabile, tutelando la salute e sicurezza dei lavoratori e garantendo la continuità di produzione e la capacità di rispondere ai problemi in modo efficace o di anticiparli.
Sono stati altresì utili tutti gli ambienti e strumenti di collaborazione a distanza, per le riunioni ordinarie e straordinarie che sono parte della vita di fabbrica, per l’analisi o le azioni puntuali, quali quelle per le fasi di collaudo o manutenzione.
Ma essere smart manufacturing cosa comporta alla propria filiera, lato supply-chain?
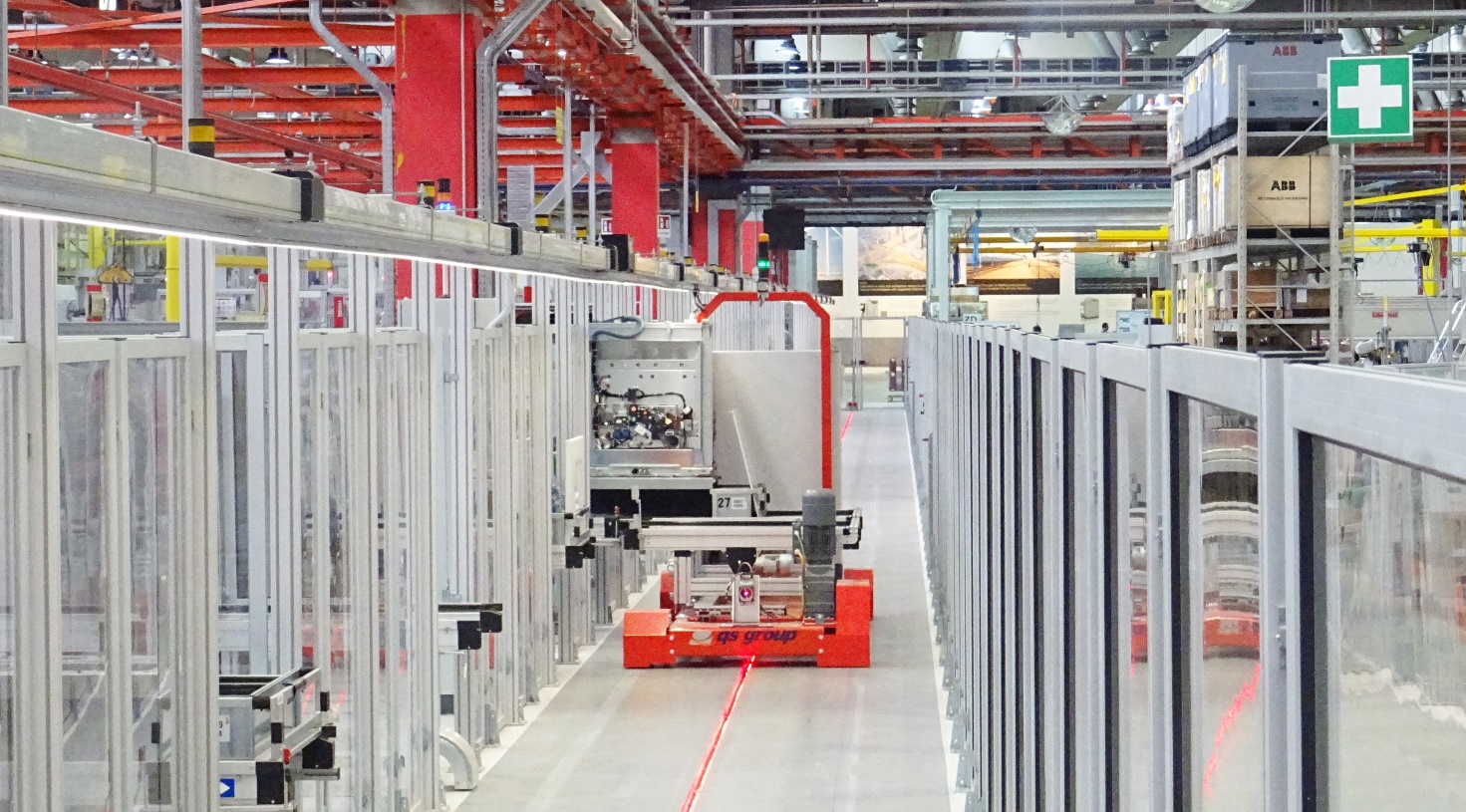
ABB Dalmine, produzione interruttori distribuzione primaria
Smart manufacturing, effetti sulla supply-chain
La strategia digitale ABB in Italia prevede significativi investimenti in competenze e tecnologie nelle fabbriche, in particolare in quelle Lighthouse Plant di Dalmine, Frosinone e Santa Palomba. I programmi intrapresi condurranno alla realizzazione di una produzione industriale ancor più automatizzata e interconnessa, nonché alla creazione di una Digital Supply Chain dinamica e collaborativa. Al fine di raggiungere questo obiettivo, ABB ha avviato un programma di assessment dei propri fornitori per valutare il livello di maturità digitale dell’intera filiera e individuare le linee di intervento al fine di creare un ecosistema integrato per aumentare ulteriormente la competitività e l’affidabilità delle proprie attività produttive.
A questo scopo sono stati presentati a luglio 2020 i risultati dell’awareness assessment della filiera dei fornitori della fabbrica ABB di Dalmine curata dal Digital Innovation Hub (DIH). Questo assessment rappresenta una delle linee di intervento verso cui le aziende Lighthouse si impegnano per promuovere la cultura del digitale. Obiettivo di questa attività è quello di scattare una fotografia sull’attuale livello di maturità digitale, per pianificare le attività di miglioramento che possano guidare una trasformazione che porti evidenti risultati in termini di competitività delle imprese. Di fatto i Lighthouse Plant sono grandi fabbriche destinate a dimostrare concretamente, anche a beneficio delle PMI (di filiera e non), che certe applicazioni industriali sono tanto necessarie quanto sostenibili per affrontare le sfide della competizione globale.
L’assessment ha interessato un campione di 17 fornitori ubicati in Lombardia, Veneto e Lazio, costituito da piccole/medie imprese, afferenti a 5 differenti categorie merceologiche. Confrontati i risultati con un campione qualificato di oltre 700 imprese che hanno effettuato la valutazione della maturità digitale tramite la rete nazionale dei DIH di Confindustria, gli indici assegnati alle aziende della filiera ABB risultano più alti della media nazionale, segno di un percorso di integrazione e allineamento già avviato nell’ultimo decennio da ABB con i propri fornitori strategici.
Poiché il percorso intrapreso da ABB richiederà anche alle aziende della filiera ulteriori investimenti, è stato altresì siglato un accordo tra ABB e UBI Banca per supportare, tramite uno specifico plafond gli investimenti dei fornitori che hanno partecipato all’assessment. Questo è un esempio virtuoso di convergenza d’intenti tra il mondo bancario e quello industriale.
Rimandando al comunicato stampa per ulteriori dettagli in merito all’assessment , da sottolineare come essere parte di un ecosistema comporti dei vantaggi a tutti i componenti dello stesso. Di fatto si innesca un effetto di contaminazione e trascinamento che influenza reciprocamente e consente anche a chi sia meno strutturato di comunque intraprendere un percorso evolutivo nell’ottica industria 4.0.
Conclusioni
Il sito di Dalmine è una realtà di smart manufacturing dove i benefici della trasformazione digitale e l’industria 4.0 sono evidenti e tangibili. Il percorso intrapreso ha innalzato produttività e competitività, confrontandosi con le sfide sia nazionali che internazionali del mercato. L’aspetto interessante che sta emergendo è la contaminazione che questo percorso intrapreso da ABB sta avendo nell’ecosistema della supply chain, che punta a essere una digital supply chain.
Discutere di smart manufacturing, industria 4.0 e delle tecnologie abilitanti tali paradigmi è sempre occasione di confronto per crescere e fare ulteriori passi evolutivi. Poter poi disporre di riferimenti non solo teorici ma reali ed operativi è un vantaggio di cui potersi avvalere per investire meglio. Essere Lighthouse Plant è motivo di orgoglio, ma anche una grande responsabilità perché solo se il tessuto industriale italiano evolve nell’ottica smart manufacturing e industria 4.0, allora riusciremo a garantire un futuro migliore al nostro paese, per tutti.
Link per approfondimenti
Smart Societies – Industries https://abbsmartsocieties.com/
Zero Emissioni https://new.abb.com/mission-to-zero
Automated Distribution Center Concept https://www.sdfocus.se/logistics/index.html
- Gli stabilimenti di Dalmine, Frosinone e Santa Palomba sono stati identificati come Lighthouse plants dal MISE nell’ambito del Piano Industria 4.0. ABB Italia, con i suoi 3 stabilimenti, si affianca a Ansaldo Energia, Tenova/Ori Martin, e Hitachi Rail Italy, formando il Lighthouse Plant Club. ↑
Articolo originariamente pubblicato il 02 Set 2020